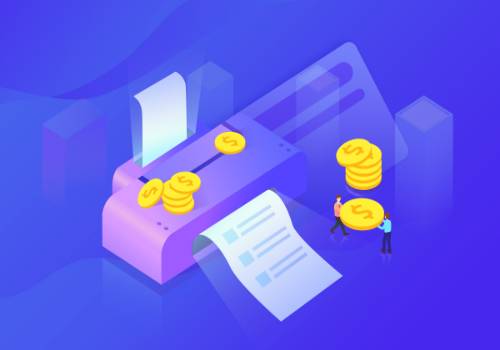
一、需求端:排放政策要求高+新能源车里程焦虑强,倒逼车企推进轻量化应用
(资料图)
“双碳”目标下,政策对于汽车百公里油耗提出要求。2020年10月,中国汽车工程学会牵头组织编制的《节能与新能源汽车技术路线图2.0》发布,对各种类型的汽车每百公里油耗提出了要求,预计在2030年,我国新能源汽车占到总销量40%,乘用车百公里油耗达3.2L,响应“双碳”目标。从燃油车角度来看,汽车的平均油耗与整车质量呈正相关,汽车轻量化对于降低传统车油耗具有积极促进作用。据研究数据,汽车重量每减轻10%,最多可实现节油5-10%;汽车整备质量每减少100千克,百公里油耗可降低0.3-0.6升。
《节能与新能源技术路线图2.0》部分要求
2025年 | 2030年 | 2035年 | |
乘用车(含新能源)新车油耗 | 4.6L/100km | 3.2L/100km | 2.0L/100km |
传统能源乘用车新车平均油耗 | 5.6L/100km | 4.8L/100km | 4L/100km |
混动新车占传统能源乘用车 | 50% | 75% | 100% |
新能源汽车占总销量 | 20% | 40% | 50% |
资料来源:观研报告网
新能源车存在较大的里程焦虑问题,轻量化需求更为迫切。根据罗兰贝格2022年的调研结果,里程焦虑仍是影响消费者购买电动车的首要原因。轻量化通过降低整车重量,可全面降低能耗和提升续航,若新能源车减重100kg,续航里程将提升10%-11%,同时降低20%的电池成本和日常损耗成本。未来在新能源车补贴政策退坡、补贴对续航里程门槛逐渐提升、终端用户里程焦虑较重的趋势下,新能源车的轻量化需求更为迫切。
根据观研报告网发布的《中国汽车轻量化行业发展趋势分析与投资前景研究报告(2023-2030年)》显示,汽车轻量化应用优势显著,解决汽车能源消耗+续航焦虑+提高性能的痛点需求。未来随着轻量化兼顾提升续航和汽车性能,迎合了驾驶舒适性/安全性/经济性的要求,在需求端刺激下有望打开市场广阔空间。
数据来源:观研报告网
我国新能源汽车补贴对续航里程门槛要求
时间 | 续航里程门槛 | 补贴政策 |
2018 | ≥150km | 按续航里程分为150-200km/200-250km/250-300km/300-400km/400km+五档,补贴金额分别为1.5w/2.4w/3.4w/4.5w/5w |
2019 | ≥250km | 按续航里程分为250-400km/400km+两档,补贴金额分别为1.8w/2.5w |
2020 | ≥300km | 按续航里程分为300-400km/400km+两档,补贴金额分别为1.62w/2.25w |
2021 | ≥300km | 按续航里程分为300-400km/400km+两档,补贴金额分别为1.3w/1.8w |
2022 | ≥300km | 按续航里程分为300-400km/400km+两档,补贴金额分别为0.91w/1.26w |
资料来源:观研报告网
二、供给端:一体化压铸突破铝合金连接工艺限制,加快汽车轻量化进程
铝合金性能优越且工艺成熟,应用性价比、量产难度、性能表现的综合表现好,中短期具有大规模使用可能性。汽车轻量化手段包括结构优化设计、制造工艺优化、轻量化材料应用,应用轻量化材料实现减重的同时兼顾了汽车综合性能的稳定,目前为主流方案。而综合考虑性价比、技术工艺、性能表现等因素,铝合金在现阶段的可行度最高,是当前最成熟、最多应用的方案。较其他材料,铝合金性能优越,减重效果好,且成本适中,在做到同等减重效果情况下,单位成本最低。同时其轻质高强,成型性强,通过挤压成型即可满足复杂架构的一次成型,符合量产需要,中短期看具备大规模使用的条件。
路线图1.0提出2020年、2025年、2030年车辆整备质量最终将实现较2015年分别减重10%/20%/35%,路线2.0进一步提高要求,2025年、2030年、2035年燃油乘用车轻量化系数降低10%/18%/25%、纯电动乘用车轻量化系数降低15%/25%/35%,技术方案变化不大。轻量化主要减重手段是使用轻量化材料,具体而言,先重点发展超高强钢技术,再重点发展铝合金技术、实现铝合金零件的批量生产和产业化应用,远期重点发展镁合金和碳纤维复合材料技术并实现大范围应用。
汽车轻量化技术发展路线图1.0
2020年 | 2025年 | 2030年 | |
车辆整备质量 | 较2015年减重10% | 较2015年减重20% | 较2015年减重35% |
高强度钢 | 强度600MPa以上的AHSS钢应用达到50% | 第三代汽车钢应用比例达到白车身重量的30% | 200MPa级以上钢材有一定比例的应用 |
铝合金 | 单车用铝量达到190kg | 单车用铝量超过250kg | 单车用铝量超过350kg |
镁合金 | 单车用镁量达到15kg | 单车用镁量达到25kg | 单车用镁量达到45kg |
碳纤维增强复合材料 | 碳纤维有一定使用量,成本比2015年降低50% | 碳纤维使用量占车重2%,成本比上一阶段降低50% | 碳纤维使用量占车重5%,成本比上一阶段降低50% |
资料来源:观研报告网
连接技术混用带来产品成本增加和效率降低,限制了铝合金在汽车的应用范围。铝合金是目前性价比较优的汽车轻量化材料,其较普通钢材可达到40%的减重率且生产工艺较成熟,根据赛瑞研究,2020年铝合金在汽车轻量化市场的占比在65%左右。但由于当前汽车材料连接工艺以冲压+机器人焊接为主,与钢材料相比,铝材料存在导热系数大易导致焊缝性能下降、合金表面氧化层污染电极、热膨胀系数高导致零件变形大等问题,制造端的冲焊工艺较困难且拼接效率低,进而导致其连接成本为钢制车身的2-3倍。
同时,随着钢、镁铝合金、碳纤维等多种材料在汽车上加速应用,材料连接工艺更为复杂,一方面加大了设备投入、增加了生产成本,一方面大量的焊接、铆接和胶接工艺大幅增加了作业时间、降低生产效率,使得减重性能更好的全铝车身在现有冲压+机器人焊接的工艺模式下难以普及。以第四代奥迪A8车身为例,其使用铝合金白车身较钢制车身降重了近30%,但需要包括点焊、激光焊、涡流焊、铆接、自切削螺钉联接、卷边等14种连接工艺,其激光焊接焊缝4.75米、包边22.01米、胶接152.94米、MIG焊点5892个、铆接2976个等,工艺复杂度远高于电阻焊为主的钢制白车身,整体工艺成本较高。
铝合金的冲焊工艺复杂导致制造成本较高
铝合金痛点 | 成因 |
材料成本高 | 铝合金材料成本是钢材的3倍左右 |
连接工艺难度与成本高 | 铝合金连接工艺:铆接、激光铆接、点焊、搅拌摩擦焊、CMT等,连接成本是钢材的2-3倍钢材连接工艺:以电阻焊为主 |
设计与生产难度高 | 铝合金需要根据新材料特性进行产品结构再设计、产品试制检测、设备模具等更新; 铝合金延伸率低,易产生裂纹,设计时要求保证形状不突变,有较高的加工难度; 铝合金材质更软,冲压回弹难控制,对生产精度和生产环境的条件要求严苛 |
资料来源:观研报告网
一体化压铸突破铝合金连接工艺限制,加速汽车轻量化发展进程。汽车制造的传统工艺分为冲压-焊装-涂装-总装四步骤,其中车身需要将各车身冲压零件焊接为发动机舱、侧围、前后底板、顶盖等分总成线,再最后合装为主焊生产线,而一体化压铸技术通过一次高压压铸成型,合并了冲压和焊装环节,将除了外覆盖件和部分悬架件以外的白车身一次压铸为大型零件。
一体化压铸工艺本质上革新了汽车轻量化工艺和材料使用,首先在制造工艺上,一体化压铸合并冲压和焊装工艺,显著简化生产流程、提高生产效率,我们看好其他主机厂在特斯拉的示范作用下不断引进一体压铸工艺,合并传统的冲压焊装工艺。其次在材料使用上,钢板易于冲压和焊装,过去广泛应用于传统的汽车制造中,铝合金是压铸的主要材质,随着一体化压铸的逐步引进,我们看好其突破材料连接工艺的限制,加速在汽车轻量化中的应用。
一体化压铸车身结构件对传统工艺的革新情况
资料来源:观研报告网
三、产业端:造车新势力引领传统车企跟进,轻量化产业进程加快
从当前各大车企的轻量化布局看,轻量化产业主要由特斯拉引领、造车新势力紧跟、传统车企加大力度布局,合力推进轻量化的产业化进程。
(1)特斯拉:作为新能源车头部持续加码新能源车轻量化,电池包和车身轻量化为重点。以Model3为例,其轻量化从电池包开始逐步拓展到车身、底盘、电子电器,整车轻量化指数在竞品中较突出。具体措施包括,采用高集成化的E平台、提升电池密度减少电芯数量、优化电池连接工艺来减少铝片用量、采用大模组设计减少组件连接件、优化电池包箱体结构、使用钢铝结合的车身、使用全铝线束、开发一体化压铸车身结构件等。
特斯拉Model3轻量化策略一览
资料来源:观研报告网
(2)造车新势力:蔚来主攻全铝车身,小鹏发力电池车身一体化技术。蔚来ET5对车身后地板使用一体化压铸工艺,后纵梁的吸能盒、轮拱等易损部位保留了单独零件设计,车身后地板减重30%;定位于豪华纯电中大型轿车的ET7采用了超高强度钢铝混合白车身,包含42%的铝/57%的钢/1%的复合材料,白车身重量约420kg,占车重1/6;ES8采用了全铝车身+7种先进连接技术,白车身仅重335kg,减重40%,底盘/悬挂/轮毂/刹车系统/电池组外壳也为全铝材质。小鹏23年发布扶摇架构采用电池车身一体化技术,节省5%的垂向车内空间。
(3)传统车企:积极布局新能源车轻量化。如大众在其全新新能源车平台MEB中使用全新车身,把电池和电机融入了车身底架,电池壳采用铝合金;比亚迪在其e平台集成了电机电控,实现了车身重量下降25%、功率密度提升20%。
汽车零部件轻量化发展布局企业
底盘轻量化 | 动力系统轻量化 |
转向节: 国内:华域汽车、拓普集团、伯利特等。 国外:Magna、ZF、Brembo等 | 动力系统: 国内:爱柯迪、旭升集团、文灿股份、广东鸿图、鸿特精密、美利信、嵘泰股份、瑞鹄模具; 国外:Pierbug、Georg、DGS等 |
副车架: 国内:华域汽车、拓普集团、万安科技、凌云股份; 国外:Chassix、Pierdug等 | |
控制臂: 国内:华域汽车、拓普集团、伯特利、旭升集团等; 国外:OTTO、FUCHS、ZF、Chassix | 铝电池盒: 国内;华域汽车、敏实集团、凌云股份、拓普集团、祥鑫科技、华达科技等; 国外:Benteler、Gestamp |
制动卡钳: 国内:华域汽车、京西国际、安陆特、伯特利等; 国外:ZF、Brembo | |
车身轻量化 | 内饰轻量化 |
热成型车身: 国内:华域汽车、凌云股份、敏实集团、宁波华翔; 国外:本特勒、海斯坦普 | 国内:华域汽车、宁波华翔、常熟汽饰; 国外:安通林、佛吉亚、麦格纳等 |
自车身焊接: 国内:安徽巨一、大连奥拓; 国外:库卡、埃斯顿等 | |
一体化压铸: 爱柯迪、文灿股份、广东鸿图、美利信、嵘泰股份、瑞鹄模具、多利科技、博俊科技 |
资料来源:观研报告网